0102030405
An in-depth visit to a customer site in Shandong was carried out to inspect equipment and facilitate technical exchanges, helping to upgrade the customer's production line
2025-06-30
To further improve customer service and ensure the efficient and stable operation of the equipment, the technical team from Beijing Lonco recently visited the production workshop of a key customer in Shandong. They carried out regular equipment inspections and debugging, and held a symposium on connection issues for the new production line that the customer is set to launch. The technical team also held a symposium on the interface of the new production line to be put into operation. This service reflects the company's customer-centred approach and provides solid technical support for the customer's subsequent capacity upgrade.
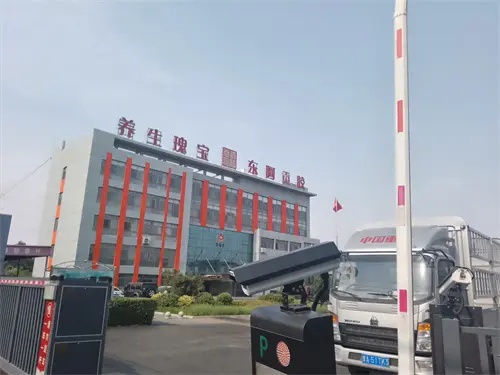
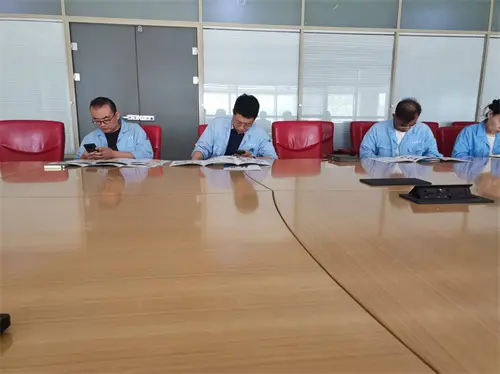
Professional inspection and escort production on-site debugging to guarantee efficiency
In the customer's workshop, the technical team from Beijing Lonco conducted a thorough inspection of the checkweigher, Weight Sorter and conveyor that had been put into use. The engineers investigated the potential risks of the equipment one by one through precision instrument testing, operation data analysis, and practical observation. They focused on wear and tear of core components, control system stability, and optimisation of production efficiency indicators. After eight consecutive hours of meticulous work, the team successfully solved the intermittent jamming problem in the transmission system reported by the customer and carried out preventive maintenance on the lubrication module. This improved the equipment's overall efficiency by 12%. The manager of the customer's workshop, Mr Wang, said: "Lonco's technical team is very professional, and each inspection uncovers details that we had overlooked in our daily maintenance. After this debugging, the failure rate of the equipment has dropped significantly, providing us with the means to reach our quarterly production target.”
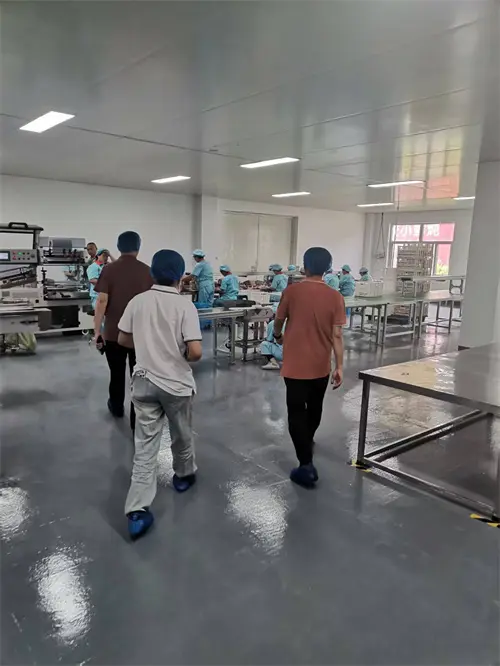
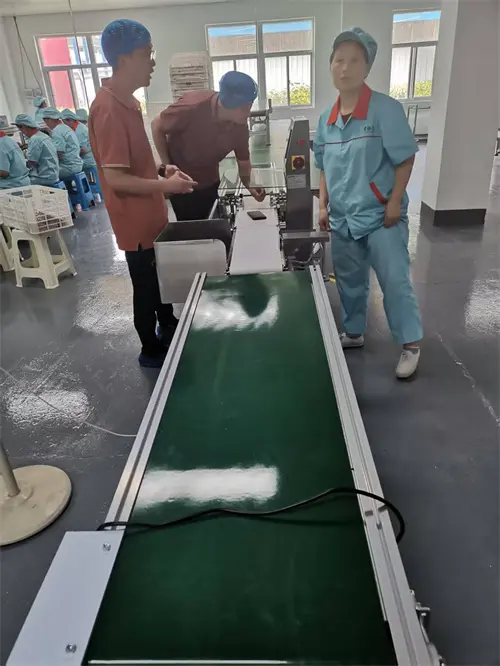
Focusing on the demand for a new line and complicated intelligent upgrades
As the customer's production capacity expansion plan advances, a brand new automated production line will soon be constructed. To this end, Beijing Lonco organised a seminar for the technical team and the people in charge of the customer's production, purchasing and R&D departments. The meeting focused on the compatibility of new and old production line equipment, data interoperability structures, and intelligent transformation plans. At the meeting, Mr Zhang, Technical Director at Beijing Lonco, systematically analysed the key connection points between the existing equipment and the new production line and proposed a "phase-by-phase adaptation" solution. Given the high-precision requirements of the new production line, it was recommended that a modular design be adopted and that 15% expansion redundancy be reserved to cope with future technological upgrades. The customer recognised the value of this solution, and the two parties reached a preliminary agreement on equipment upgrades worth over 500,000 RMB. After the meeting, Mr Li, the customer's Chief Technical Engineer, said, “Lonco not only provides equipment, but also understands how to make the old and new production lines ‘talk’. The solution this time has taken cost control and foresight into account, which gives us more confidence in the intelligent transformation.”
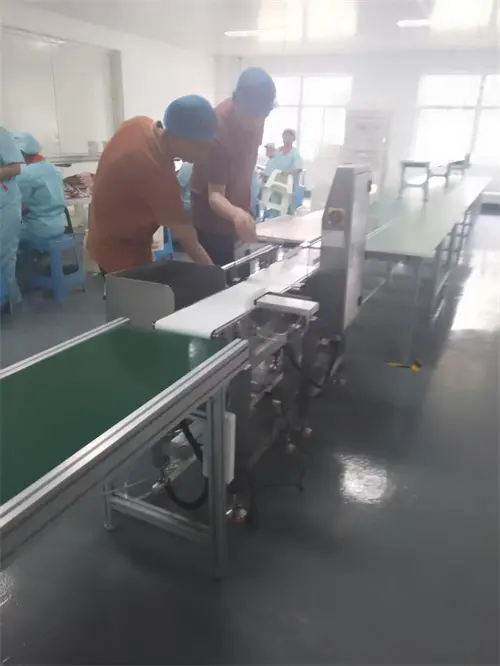
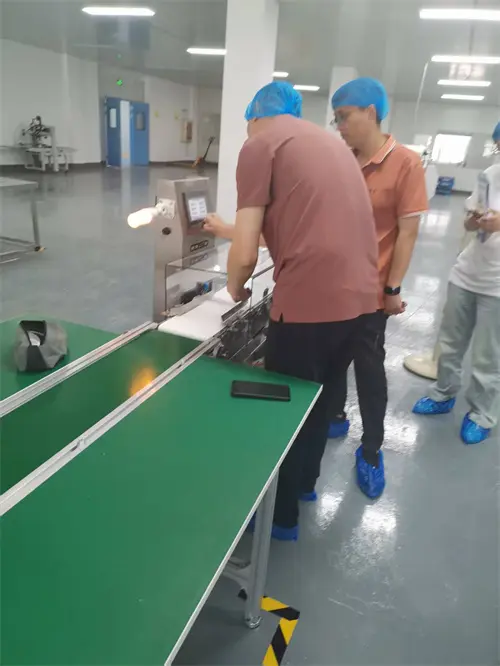
Service empowers manufacturing and innovation drives the future
This trip to Shandong is an important part of the “Customer Deep Plowing Program” launched by Beijing Lanxess in 2025. As a leading enterprise in China's automation and intelligent equipment sector, focusing on Weighing, packaging, testing and sorting solutions, and with products covering automated production lines and industrial scales, Lonco has provided technical support to over 200 manufacturing enterprises nationwide. This support is delivered through a full-cycle service system comprising regular inspections, quick responses and customised solutions. We have provided technical support to over 200 manufacturing enterprises in China.